鉴定背景
在智能制造快速发展的时代,激光切割设备以其高精度、高效率、非接触加工等优势,广泛应用于汽车制造、航空航天、电子电器、五金加工等众多领域。从汽车车身零部件的精密切割,到航空航天领域复杂结构件的加工,激光切割设备的质量直接影响产品的加工精度、生产效率和企业经济效益。然而,随着市场需求的增长,激光切割设备生产厂家不断涌现,设备质量良莠不齐。部分设备存在激光功率不稳定、切割精度不足、安全防护措施不到位等问题,不仅导致加工产品质量缺陷,还可能引发火灾、激光灼伤等安全事故。因此,开展激光切割设备质量鉴定工作,成为保障生产安全、提升产品质量、规范市场秩序的关键环节。
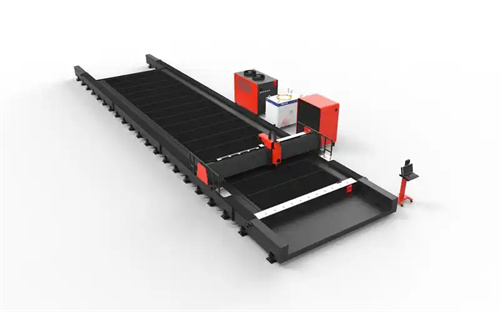
鉴定范围
(一)激光发生系统
1. 激光发生器故障:激光发生器可能出现功率输出不稳定的情况,导致切割过程中时而切割不透,时而过度烧蚀材料,影响切割质量。这可能是由于激光发生器内部的泵浦源老化、谐振腔镜片污染或损坏、冷却系统故障等原因造成。例如,泵浦源能量输出下降,无法为激光产生提供足够的能量;谐振腔镜片表面沾染灰尘或出现划痕,会降低激光的反射和聚焦效率,使激光功率衰减。
2. 激光光束质量差:激光光束的模式、发散角等参数不符合要求,会导致切割边缘粗糙、切口宽度不均匀。不良的光束质量可能是激光发生器内部光学元件安装调试不当,或者长期使用后元件性能下降所致。比如,聚焦透镜的焦距偏差、位置偏移,会使激光光束无法准确聚焦在材料表面,影响切割效果。
(二)数控系统
1. 控制精度不足:数控系统在控制激光切割头的运动轨迹时,存在定位误差和重复定位误差,导致切割出的工件尺寸不符合设计要求。这可能是由于数控系统的伺服电机性能不佳、传动机构(如丝杠、导轨)精度下降,或者数控系统的软件算法存在缺陷。例如,伺服电机的编码器故障,会使电机的实际转速与数控系统指令不一致,从而造成切割头运动偏差;丝杠的螺距误差积累,会随着切割长度的增加,导致定位误差不断增大。
2. 软件功能缺陷:数控系统的操作软件可能存在界面不友好、操作流程复杂,影响操作人员的工作效率。同时,软件在处理复杂图形的切割路径规划时,可能出现算法不合理的情况,导致切割路径过长、空行程过多,降低切割效率。此外,软件还可能存在与激光发生器、辅助气体控制系统等设备的通信故障,无法实现协同工作。
(三)机械结构
1. 传动部件磨损:激光切割设备的传动机构,如直线导轨、滚珠丝杠、齿轮齿条等,在长期运行过程中会因摩擦产生磨损。导轨的磨损会导致切割头运动时的直线度下降,使切割轨迹出现偏差;丝杠的磨损会影响其传动精度,造成定位不准确。例如,导轨表面的润滑不足,会加剧摩擦,加速导轨的磨损;丝杠螺母副的间隙增大,会使切割头在启停过程中出现窜动,影响切割精度。
2. 机械结构变形:设备在运输过程中的碰撞、安装时的地基不平,或者长期高负荷运行,都可能导致机械结构发生变形。龙门式激光切割机的横梁变形,会使切割头在沿横梁移动时,距离材料表面的高度发生变化,影响激光的聚焦效果;床身的变形会导致整个设备的稳定性下降,产生振动,进而影响切割质量。
(四)辅助系统
1. 辅助气体供应问题:辅助气体的压力不稳定、流量不足或气体纯度不达标,都会影响切割效果。在切割金属材料时,氧气作为辅助气体,若压力不足,无法将熔化的金属及时吹离切口,会导致切口挂渣;氮气纯度不够,会在切割不锈钢等材料时,使切口表面氧化变色,影响产品质量。此外,气体管路存在泄漏、堵塞,或者气体阀门控制失灵,也会导致辅助气体供应异常。
2. 排烟除尘系统故障:激光切割过程中会产生大量的烟尘和有害气体,如果排烟除尘系统吸力不足,无法及时将这些污染物排出,会污染工作环境,危害操作人员的身体健康。同时,烟尘附着在光学元件表面,会影响激光的传输和聚焦,降低激光功率,缩短光学元件的使用寿命。排烟管道堵塞、风机故障、过滤装置失效等,都可能导致排烟除尘系统无法正常工作。
(五)安全防护系统
1. 激光防护措施不到位:激光切割设备的防护罩存在破损、密封不严的情况,会使激光泄露,对操作人员造成眼睛和皮肤的伤害。防护罩的观察窗如果透光率不符合要求,或者没有配备合适的滤光镜片,操作人员在观察切割过程时,也会受到激光的潜在威胁。此外,设备的联锁装置失效,在防护罩打开时,激光仍能发射,存在极大的安全隐患。
2. 电气安全隐患:设备的电气系统如果接地不良,当发生漏电时,会使设备外壳带电,危及操作人员的生命安全。电气线路绝缘层老化、破损,容易引发短路,甚至导致火灾事故。另外,设备的急停按钮如果失灵,在遇到紧急情况时,无法迅速停止设备运行,可能会造成更严重的后果。
鉴定标准
激光切割设备质量鉴定依据多项国家标准和行业标准。在激光性能方面,《激光设备 激光辐射安全、设备分类、要求和用户指南》(GB 7247.1)对激光设备的辐射安全、分类等作出规定,确保激光设备在使用过程中的安全性;《激光切割 第 1 部分:术语和符号》(GB/T 18415.1)统一了激光切割领域的术语和符号,为技术交流和标准执行提供基础。关于数控系统,《工业自动化系统与集成 数控 第 1 部分:机床数字控制装置通用技术条件》(GB/T 3167)规定了数控装置的技术要求、试验方法等,保障数控系统的可靠性和精度。在机械结构方面,《金属切削机床 精度检验通则 第 1 部分:几何精度检验》(GB/T 17421.1)适用于激光切割设备机械结构的几何精度检验,确保机械结构的稳定性和加工精度。对于辅助系统和安全防护系统,也有相应的标准,如《机械安全 防护装置 固定式和活动式防护装置设计与制造一般要求》(GB/T 8196)对设备的安全防护装置提出要求,保障操作人员的安全。这些标准为激光切割设备质量鉴定提供了全面、科学的依据。
鉴定方法
(一)激光发生系统
1. 激光发生器故障:激光发生器可能出现功率输出不稳定的情况,导致切割过程中时而切割不透,时而过度烧蚀材料,影响切割质量。这可能是由于激光发生器内部的泵浦源老化、谐振腔镜片污染或损坏、冷却系统故障等原因造成。例如,泵浦源能量输出下降,无法为激光产生提供足够的能量;谐振腔镜片表面沾染灰尘或出现划痕,会降低激光的反射和聚焦效率,使激光功率衰减。
2. 激光光束质量差:激光光束的模式、发散角等参数不符合要求,会导致切割边缘粗糙、切口宽度不均匀。不良的光束质量可能是激光发生器内部光学元件安装调试不当,或者长期使用后元件性能下降所致。比如,聚焦透镜的焦距偏差、位置偏移,会使激光光束无法准确聚焦在材料表面,影响切割效果。
(二)数控系统
1. 控制精度不足:数控系统在控制激光切割头的运动轨迹时,存在定位误差和重复定位误差,导致切割出的工件尺寸不符合设计要求。这可能是由于数控系统的伺服电机性能不佳、传动机构(如丝杠、导轨)精度下降,或者数控系统的软件算法存在缺陷。例如,伺服电机的编码器故障,会使电机的实际转速与数控系统指令不一致,从而造成切割头运动偏差;丝杠的螺距误差积累,会随着切割长度的增加,导致定位误差不断增大。
2. 软件功能缺陷:数控系统的操作软件可能存在界面不友好、操作流程复杂,影响操作人员的工作效率。同时,软件在处理复杂图形的切割路径规划时,可能出现算法不合理的情况,导致切割路径过长、空行程过多,降低切割效率。此外,软件还可能存在与激光发生器、辅助气体控制系统等设备的通信故障,无法实现协同工作。
(三)机械结构
1. 传动部件磨损:激光切割设备的传动机构,如直线导轨、滚珠丝杠、齿轮齿条等,在长期运行过程中会因摩擦产生磨损。导轨的磨损会导致切割头运动时的直线度下降,使切割轨迹出现偏差;丝杠的磨损会影响其传动精度,造成定位不准确。例如,导轨表面的润滑不足,会加剧摩擦,加速导轨的磨损;丝杠螺母副的间隙增大,会使切割头在启停过程中出现窜动,影响切割精度。
2. 机械结构变形:设备在运输过程中的碰撞、安装时的地基不平,或者长期高负荷运行,都可能导致机械结构发生变形。龙门式激光切割机的横梁变形,会使切割头在沿横梁移动时,距离材料表面的高度发生变化,影响激光的聚焦效果;床身的变形会导致整个设备的稳定性下降,产生振动,进而影响切割质量。
(四)辅助系统
1. 辅助气体供应问题:辅助气体的压力不稳定、流量不足或气体纯度不达标,都会影响切割效果。在切割金属材料时,氧气作为辅助气体,若压力不足,无法将熔化的金属及时吹离切口,会导致切口挂渣;氮气纯度不够,会在切割不锈钢等材料时,使切口表面氧化变色,影响产品质量。此外,气体管路存在泄漏、堵塞,或者气体阀门控制失灵,也会导致辅助气体供应异常。
2. 排烟除尘系统故障:激光切割过程中会产生大量的烟尘和有害气体,如果排烟除尘系统吸力不足,无法及时将这些污染物排出,会污染工作环境,危害操作人员的身体健康。同时,烟尘附着在光学元件表面,会影响激光的传输和聚焦,降低激光功率,缩短光学元件的使用寿命。排烟管道堵塞、风机故障、过滤装置失效等,都可能导致排烟除尘系统无法正常工作。
(五)安全防护系统
1. 激光防护措施不到位:激光切割设备的防护罩存在破损、密封不严的情况,会使激光泄露,对操作人员造成眼睛和皮肤的伤害。防护罩的观察窗如果透光率不符合要求,或者没有配备合适的滤光镜片,操作人员在观察切割过程时,也会受到激光的潜在威胁。此外,设备的联锁装置失效,在防护罩打开时,激光仍能发射,存在极大的安全隐患。
2. 电气安全隐患:设备的电气系统如果接地不良,当发生漏电时,会使设备外壳带电,危及操作人员的生命安全。电气线路绝缘层老化、破损,容易引发短路,甚至导致火灾事故。另外,设备的急停按钮如果失灵,在遇到紧急情况时,无法迅速停止设备运行,可能会造成更严重的后果。
鉴定流程
(一)委托受理
当激光切割设备出现质量争议、故障问题或需要进行质量评估时,委托方(企业、个人或相关机构)向具备资质的鉴定机构提出鉴定申请。委托方需填写详细的委托申请表,提供设备的基本信息,包括设备品牌、型号、购买时间、使用场所、故障现象描述等,并提交设备的使用说明书、安装调试记录、维护保养记录、维修记录等相关资料。鉴定机构收到申请后,对委托事项进行初步审查,评估鉴定的可行性和自身的承接能力。若符合受理条件,与委托方签订鉴定委托合同,明确鉴定目的、范围、费用、完成时间等双方权利和义务。
(二)鉴定准备
鉴定机构组建专业的鉴定团队,团队成员应具备激光技术、数控技术、机械工程、电气自动化等相关专业知识和丰富的实践经验。鉴定团队深入研究委托方提供的资料,熟悉激光切割设备的工作原理、技术参数和使用情况。根据设备特点和鉴定要求,制定详细的鉴定方案,确定鉴定依据的标准、采用的鉴定方法、所需的仪器设备、人员分工和时间安排。对所需的检测仪器设备进行校准和调试,确保其精度和准确性满足鉴定需求,并准备好相关工具和安全防护用品。与委托方沟通协调,确定现场鉴定的具体时间、地点和配合事项。
(三)现场勘查与检测
鉴定人员携带仪器设备前往设备现场,首先对设备的安装环境、运行状况进行全面检查和记录,包括设备安装位置是否符合要求、周围是否有电磁干扰源、电源电压是否稳定等。与设备操作人员、维护人员交流,了解设备的日常使用频率、故障发生前后的现象、维护保养历史等信息。按照鉴定方案,对激光切割设备进行外观检查、性能测试、机械性能测试、辅助系统测试和安全性能测试等各项检测工作。在检测过程中,严格遵守操作规程,详细记录检测数据、现象和问题,对关键部位进行拍照、录像留存证据。若现场发现设备存在安全隐患,及时采取措施消除隐患,确保鉴定工作的安全进行。
(四)数据分析与评估
现场检测结束后,鉴定人员对获取的检测数据进行整理、分析。将测试数据与相关标准、设备技术参数进行对比,判断激光切割设备各项性能指标是否达标。针对发现的质量问题,运用专业知识和经验,分析问题产生的原因,可能涉及设计缺陷、制造工艺问题、原材料质量、使用维护不当等方面。若遇到疑难问题,组织专家进行研讨、论证,必要时进行补充检测或模拟试验。根据数据分析和原因分析结果,对激光切割设备的质量状况进行综合评估,明确设备是否存在质量问题、问题的严重程度以及对使用性能和安全性的影响。
(五)出具鉴定报告
根据数据分析与评估结论,鉴定机构撰写鉴定报告。报告内容包括委托方信息、设备基本信息、鉴定目的、鉴定依据、鉴定过程与方法、检测数据、分析评估结论、处理建议等。鉴定报告需经过严格的内部审核流程,由项目负责人、技术负责人等专业人员审核,确保报告内容完整、数据准确、结论客观公正。审核通过后,由具备资质的鉴定人员签字,并加盖鉴定机构公章。将鉴定报告交付委托方,并根据委托方需求,对报告内容进行详细解释说明。同时,按照规定对鉴定过程中的原始记录、数据、照片等资料进行归档保存,以备后续查阅。
|